Dårlig vannmotstand, ujevn overflate, høyt pulverinnhold og ujevn lengde?Vanlige problemer og forbedringstiltak i akvatisk fôrproduksjon
I vår daglige produksjon av akvatisk fôr har vi støtt på noen problemer fra ulike sider.Her er noen eksempler å diskutere med alle, som følger:
1, Formel
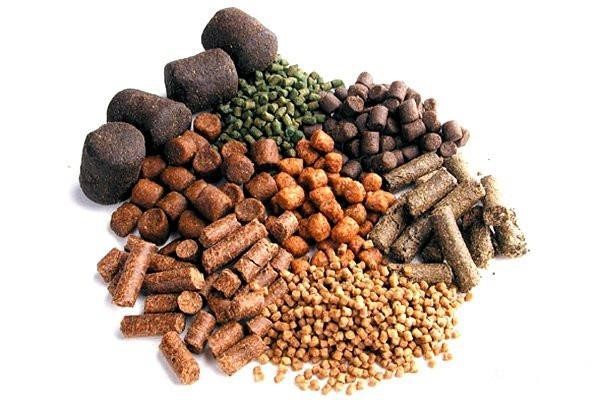
1. I formelstrukturen til fiskefôr er det flere typer melråvarer, som rapsmel, bomullsmel osv. som tilhører råfiber.Noen oljefabrikker har avansert teknologi, og oljen stekes i utgangspunktet tørr med svært lite innhold.Dessuten er disse typer råvarer ikke lett absorberende i produksjonen, noe som har stor innvirkning på granulering.I tillegg er bomullsmel vanskelig å knuse, noe som påvirker effektiviteten.
2. Løsning: Bruken av rapskake er økt, og høykvalitets lokale råvarer som riskli er tilsatt formelen.I tillegg er hvete, som utgjør omtrent 5-8 % av formelen, tilsatt.Gjennom justering er granuleringseffekten i 2009 relativt ideell, og avlingen per tonn har også økt.2,5 mm partiklene er mellom 8-9 tonn, en økning på nesten 2 tonn sammenlignet med tidligere.Utseendet til partiklene er også betydelig forbedret.
I tillegg, for å forbedre effektiviteten av å knuse bomullsfrømel, blandet vi bomullsfrømel og rapsmel i forholdet 2:1 før vi knuser.Etter forbedring var knusehastigheten i utgangspunktet på nivå med knusehastigheten til rapsmel.
2, Ujevn overflate av partikler
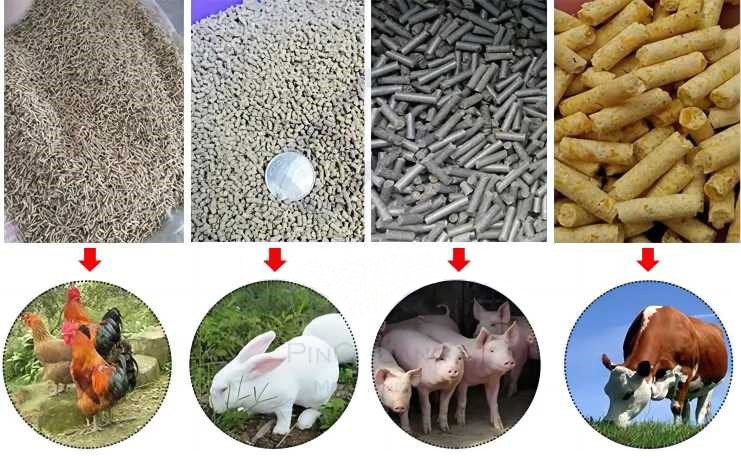
1. Det har stor innvirkning på utseendet til det ferdige produktet, og når det tilsettes vann, er det utsatt for å kollapse og har lav utnyttelsesgrad.Hovedårsaken er:
(1) Råvarene knuses for grovt, og under herdingsprosessen er de ikke helt modne og mykne, og kan ikke godt kombineres med andre råvarer når de passerer gjennom formhullene.
(2) I fiskefôrformelen med høyt innhold av råfiber, på grunn av tilstedeværelsen av dampbobler i råmaterialet under herdingsprosessen, sprekker disse boblene på grunn av trykkforskjellen mellom innsiden og utsiden av formen under partikkelkomprimering, resulterer i ujevn overflate på partiklene.
2. Håndteringstiltak:
(1) Kontroller knuseprosessen riktig
For tiden, når vi produserer fiskefôr, bruker selskapet vårt 1,2 mm silmikropulver som bulkråstoff.Vi kontrollerer bruksfrekvensen av sikten og graden av slitasje på hammeren for å sikre finheten til knusingen.
(2) Kontroller damptrykket
I henhold til formelen, juster damptrykket rimelig under produksjon, generelt kontroller rundt 0,2.På grunn av den store mengden grove fiberråvarer i fiskefôrformelen, kreves det høykvalitets damp og rimelig herdingstid.
3, Dårlig vannmotstand av partikler
1. Denne typen problemer er den vanligste i vår daglige produksjon, vanligvis relatert til følgende faktorer:
(1) Kort tempereringstid og lav tempereringstemperatur resulterer i ujevn eller utilstrekkelig temperering, lav modningsgrad og utilstrekkelig fuktighet.
(2) Utilstrekkelig klebende materialer som stivelse.
(3) Kompresjonsforholdet til ringformen er for lavt.
(4) Oljeinnholdet og andelen råfiberråvarer i formelen er for høy.
(5) Knusing av partikkelstørrelsesfaktor.
2. Håndteringstiltak:
(1) Forbedre dampkvaliteten, juster bladvinkelen til regulatoren, forleng tempereringstiden og øk fuktighetsinnholdet i råvarene på passende måte.
(2) Juster formelen, øk passende stivelsesråvarer og reduser andelen fett og råfiberråvarer.
(3) Legg til lim om nødvendig.(Natriumbasert bentonittoppslemming)
(4) Forbedre kompresjonsforholdet tilring dø
(5) Kontroller finheten av knusing godt
4, For høyt pulverinnhold i partikler
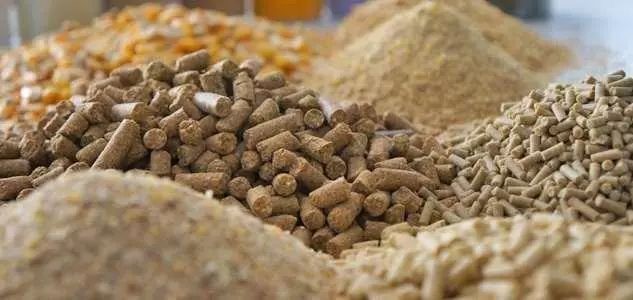
1. Det er vanskelig å sikre utseendet til generelt pelletsfôr etter avkjøling og før sikting.Kunder har rapportert at det er mer fin aske og pulver i pellets.Basert på analysen ovenfor tror jeg det er flere årsaker til dette:
A. Partikkeloverflaten er ikke glatt, snittet er ikke pen, og partiklene er løse og utsatt for pulverproduksjon;
B. Ufullstendig skjerming ved sortering av skjerm, tilstoppet skjermnett, alvorlig slitasje på gummikuler, feilaktig skjermmaskeåpning, etc;
C. Det er mye fin askerester i ferdigvarelageret, og klareringen er ikke grundig;
D. Det er skjulte farer ved fjerning av støv under pakking og veiing;
Håndteringstiltak:
A. Optimaliser formelstrukturen, velg ringformingen rimelig, og kontroller kompresjonsforholdet godt.
B. Under granuleringsprosessen kontrollerer du tempereringstiden, fôringsmengden og granuleringstemperaturen for å modne og myke opp råvarene.
C. Sørg for at partikkeltverrsnittet er pent og bruk en myk skjærekniv laget av stålbånd.
D. Juster og vedlikehold graderingsskjermen, og bruk en rimelig skjermkonfigurasjon.
E. Bruk av sekundær screeningsteknologi under det ferdige produktlageret kan i stor grad redusere pulverinnholdsforholdet.
F. Det er nødvendig å rengjøre det ferdige produktlageret og kretsen i tide.I tillegg er det nødvendig å forbedre emballasjen og støvfjerningsanordningen.Det er best å bruke undertrykk for fjerning av støv, noe som er mer ideelt.Spesielt under pakkeprosessen bør emballasjearbeideren regelmessig banke og rense støvet fra bufferbeholderen på emballasjevekten.
5, Partikkellengden varierer
1. I daglig produksjon møter vi ofte problemer med kontroll, spesielt for modeller over 420. Årsakene til dette er grovt oppsummert som følger:
(1) Fôringsmengden for granulering er ujevn, og tempereringseffekten svinger sterkt.
(2) Inkonsekvent gap mellom formrullene eller sterk slitasje på ringformen og trykkrullene.
(3) Langs ringformens aksiale retning er utløpshastigheten i begge ender lavere enn i midten.
(4) Det trykkreduserende hullet i ringformen er for stort, og åpningshastigheten er for høy.
(5) Plasseringen og vinkelen til skjærebladet er urimelig.
(6) Granuleringstemperatur.
(7) Typen og den effektive høyden (bladbredde, bredde) til ringskjærebladet har innvirkning.
(8) Samtidig er fordelingen av råvarer inne i kompresjonskammeret ujevn.
2. Kvaliteten på fôr og pellets blir generelt analysert basert på deres indre og ytre kvaliteter.Som produksjonssystem er vi mer utsatt for ting knyttet til ytre kvalitet på fôrpellets.Fra et produksjonsperspektiv kan faktorene som påvirker kvaliteten på akvatiske fôrpellets grovt oppsummeres som følger:
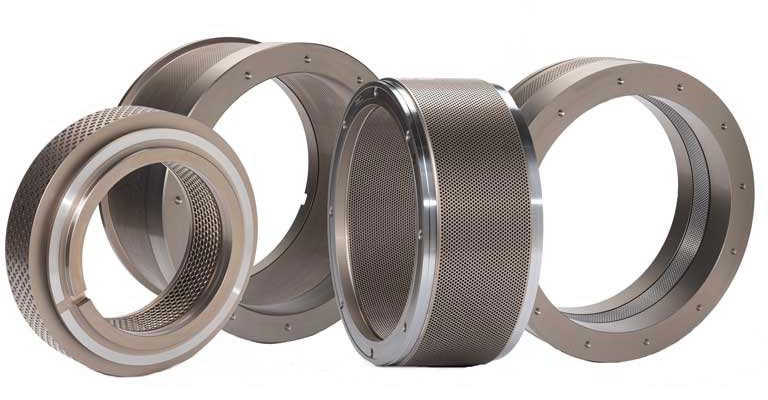
(1) Utformingen og organiseringen av formler har en direkte innvirkning på kvaliteten til akvatiske fôrpellets, og utgjør omtrent 40 % av totalen;
(2) Intensiteten av knusing og ensartethet av partikkelstørrelse;
(3) Ringformens diameter, kompresjonsforhold og lineære hastighet har innvirkning på lengden og diameteren til partikler;
(4) Kompresjonsforholdet, lineær hastighet, bråkjølings- og tempereringseffekten til ringformen, og skjærebladets innflytelse på lengden av partiklene;
(5) Fuktighetsinnholdet i råvarer, tempereringseffekt, kjøling og tørking har innvirkning på fuktighetsinnholdet og utseendet til ferdige produkter;
(6) Selve utstyret, prosessfaktorer og bråkjølings- og tempereringseffekter har innvirkning på partikkelpulverinnholdet;
3. Håndteringstiltak:
(1) Juster lengden, bredden og vinkelen på stoffskrapen, og bytt ut den slitte skrapen.
(2) Vær oppmerksom på å justere posisjonen til skjærebladet i tide i begynnelsen og nær slutten av produksjonen på grunn av den lille matemengden.
(3) Sørg for stabil fôringshastighet og damptilførsel under produksjonsprosessen.Hvis damptrykket er lavt og temperaturen ikke kan stige, bør det justeres eller stoppes i tide.
(4) Rimelig justere gapet mellomrulleskall.Følg den nye formen med nye ruller, og reparer umiddelbart den ujevne overflaten på trykkrullen og ringformen på grunn av slitasje.
(5) Reparer styrehullet til ringformen og rengjør umiddelbart det blokkerte formhullet.
(6) Når du bestiller ringformen, kan kompresjonsforholdet til de tre hullradene i begge ender av aksialretningen til den originale ringformen være 1-2 mm mindre enn det i midten.
(7) Bruk en myk skjærekniv, med en tykkelse kontrollert mellom 0,5-1 mm, for å sikre en skarp kant så mye som mulig, slik at den er på inngrepslinjen mellom ringformen og trykkrullen.
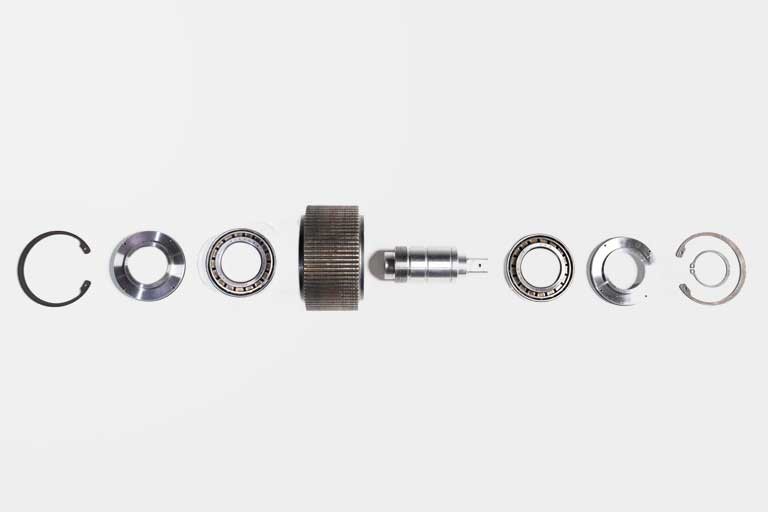
(8) Sørg for konsentrisiteten til ringformen, kontroller regelmessig spindelklaringen til granulatoren, og juster den om nødvendig.
6, Sammendrag Kontrollpunkter:
1. Sliping: Finheten til sliping må kontrolleres i henhold til spesifikasjonskravene
2. Blanding: Ensartetheten av råstoffblandingen må kontrolleres for å sikre passende blandingsmengde, blandetid, fuktighetsinnhold og temperatur.
3. Modning: Trykk, temperatur og fuktighet til puffemaskinen må kontrolleres
Størrelsen og formen på partikkelmaterialet: passende spesifikasjoner for kompresjonsformer og skjæreblader må velges.
5. Vanninnhold i ferdigfôr: Det er nødvendig å sikre tørke- og avkjølingstiden og temperaturen.
6. Oljesprøyting: Det er nødvendig å kontrollere den nøyaktige mengden oljesprøyting, antall dyser og kvaliteten på oljen.
7. Siling: Velg størrelsen på silen i henhold til materialets spesifikasjoner.
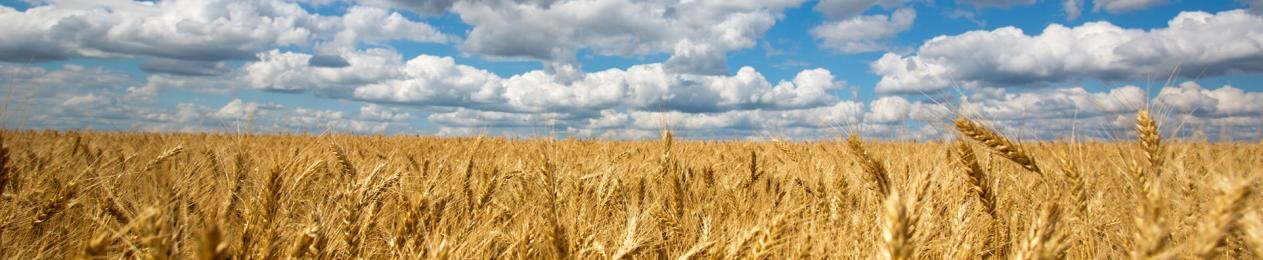
Innleggstid: 30. november 2023